Introduction
Consumers, businesses, and governments have a growing interest in “going green.” From recycling to emissions reduction to water conservation, everyone is looking for ways to limit their impact on the environment. Car, truck, and other vehicle manufacturers have become leaders in this push, which means fuel-efficiency and advancements in electric cars are sought-after goals for consumers and corporations alike.
In this guide, we’ll look at some of the critical applications evolving to help the industry reach these goals.
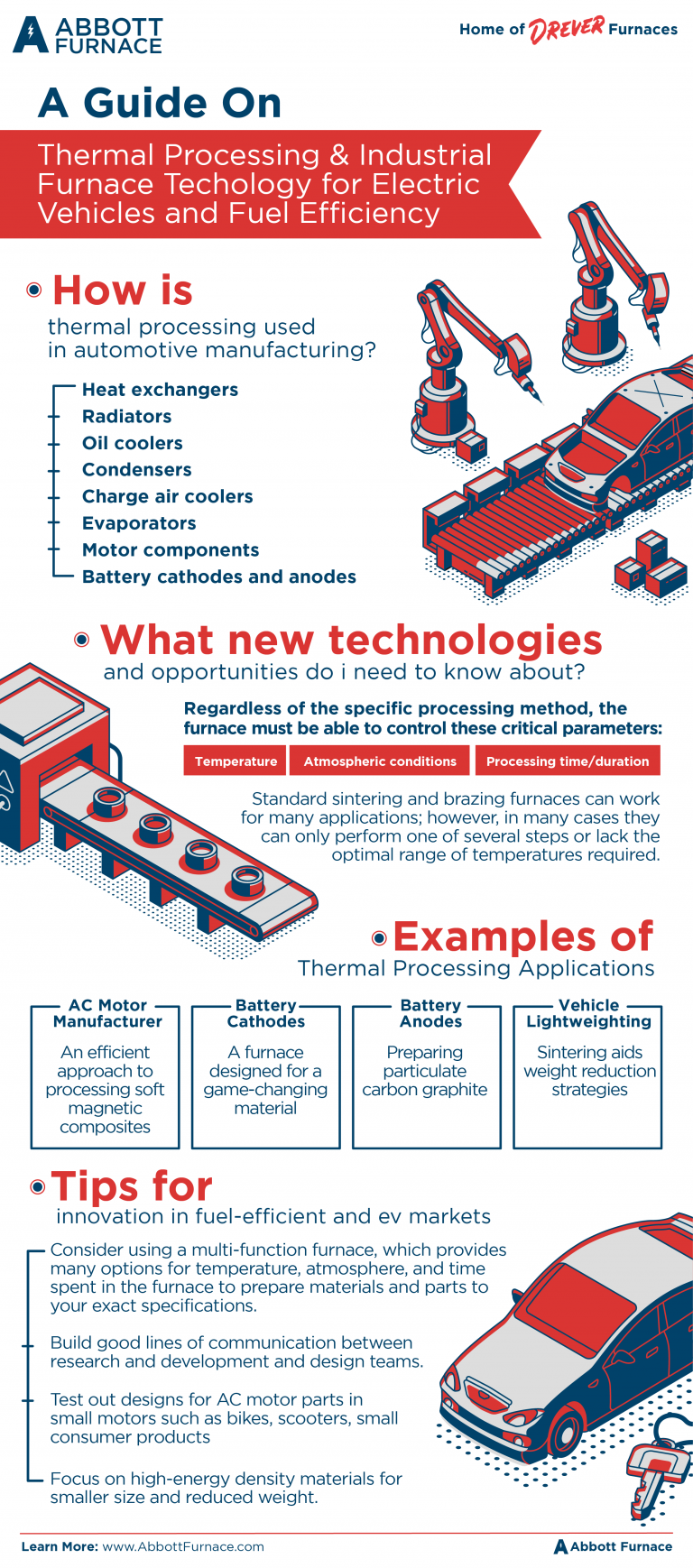
How is thermal processing used in Automotive Manufacturing?
Different types of thermal processing have been used in automotive component manufacturing for decades to prepare materials, parts, and assemblies for numerous applications, such as:
- Heat exchangers
- Radiators
- Oil coolers
- Condensers
- Charge air coolers
- Evaporators
- Motor components
- Battery cathodes and anodes
In these applications, thermal processes such as sintering, brazing, Controlled Atmosphere Brazing (CAB), and annealing are used to produce improved strength, stability, and other mechanical properties in both solid and powder metal materials and parts.
WHAT NEW TECHNOLOGIES AND OPPORTUNITIES DO I NEED TO KNOW ABOUT?
Most thermal processing is done in industrial furnaces. Regardless of the specific processing method, the furnace must be able to control these critical parameters:
- Temperature
- Atmospheric conditions
- Processing time/duration
Standard sintering and brazing furnaces can work for many applications; however, in many cases they can only perform one of several steps or lack the optimal range of temperatures required.
In these situations, it’s possible to develop multi-function furnaces tailored to the desired process and output. For example, they can be designed to vary temperatures and atmosphere in different chambers as parts or materials are conveyed through the machine. This streamlines the manufacturing process, saves time, and increases production volume while providing precise conditions for consistent quality.
THE TRANSPORTATION INDUSTRY IS ALWAYS EVOLVING
In the case of fuel-efficient and EV vehicle developments, manufacturers are looking for ways to make lighter, efficient vehicles, and rechargeable batteries with higher energy-density, longer range, and faster charging times.
And of course, the more options and tools you have for materials and methods, the better positioned you are to create new opportunities for your company. Industries with much to gain from exploring new materials and thermal processes include:
- Automotive
- Motorcycles
- Electrified bicycles/scooters
- Aviation
- Electric motors and actuators (such as those in appliances, vehicles, industrial equipment, pumps, etc.)
- Rechargeable batteries
You can gain an edge among your competitors by finding new ways to make existing components that are smaller and lighter, or that can be used in fuel-efficient internal combustion engine (ICE) and EV cars and trucks as well as energy-efficient machinery.
WHY DOES THERMAL PROCESSING MATTER IN FUEL-EFFICIENCY AND EV INNOVATIONS?
In the race to develop a better “green” vehicle, some parts, assemblies, and entire vehicle systems will change or be swapped for new designs. Examples include battery packs instead of gas tanks or parts made with additive manufacturing instead of conventional metal forming operations.
In other cases, existing parts are redesigned to be smaller, lighter, energy efficient, or energy dense. The goal is to make vehicles that require less energy to power, and to maximize driving range.
Manufacturing tools, methods, and materials change too. One example is the redesign of industrial furnaces to provide higher throughput and quality and, in some cases, the ability to use new materials altogether.
WHICH FURNACE IS BEST FOR AUTOMOTIVE APPLICATIONS?
The best furnace is the one that controls the necessary parameters. Sometimes that’s a standard furnace, other times it takes a unique, customized design that incorporates specifics for instance:
- Temperature range
- Amount of time spent in the furnace
- Atmospheric conditions
- Travel speed through the machine
- Belt width
- Multiple zones and capabilities matched to different parts of the process
- Options for optimizing workflow and cycle time
- Automated loading/unloading
- Material handling robotics
EXAMPLES OF THERMAL PROCESSING APPLICATIONS
In the rush to create the next innovation in vehicle technology, thermal processing with industrial furnaces plays a large role for AC motor components, rechargeable battery cathodes and anodes, and lightweighting. New and more efficient processes for manufacturing these are possible thanks to new developments in thermal processing methods and furnace design.
These are just a few examples of how furnaces can be designed to achieve very specific ends.
1. AC MOTOR MANUFACTURING: AN EFFICIENT APPROACH TO PROCESSING SOFT MAGNETIC COMPOSITES
>> Click here to watch this information >>
AC motors have been evolving for many years. Most recently, manufacturers have been developing and refining these motor designs in electric bicycles and scooters. These motors can also be used in cars and trucks, motorcycles, appliances, industrial equipment, pumps, and other products that use actuators and small motors.
Traditionally, the non-moving part of the motor (i.e., the stator) is wrapped with metal coils or several layers of thin, laminated metal. When current passes through the coils or metal layers, it creates the push/pull magnetic force that causes the rotor to spin inside the stator.
An alternative method is to make the stator out of soft magnetic composites. This results in a smaller yet more energy dense and powerful motor. This approach reduces vehicle weight and either improves fuel economy, or in the case of a BEV, driving range.
SOLVING MANUFACTURING CHALLENGES WITH A REDESIGNED SINTERING FURNACE
One of the biggest challenges with soft magnetic composites is removing the lubricant completely and efficiently from the compacts. Conventional sintering furnaces are used for this; however, they risk heating the parts too quickly or too hot, which creates damaging soot. Lower temperatures avoid the sooting but often require multiple passes through the furnace, which slows the manufacturing process.
By redesigning furnaces with convective heat transfer, single pass lubricant removal, and in-line curing, the process becomes significantly more efficient.
2. BATTERY CATHODES: A FURNACE DESIGNED FOR A GAME-CHANGING MATERIAL
Batteries are composed of a cathode and an anode, usually bars or strips of metal, submerged in an electrolyte solution. In an alternative technology, solid-state batteries replace the electrolytic solution with a thin polymer layer. Batteries are usually formed into discs and stacked or thin layers that are rolled into a cylinder.
Cathode material in lithium-ion batteries is commonly made of a lithium-cobalt combination. This material in lithium-ion batteries is effective, yet it is challenging to produce due to the high cost and limited availability of cobalt.
One potential alternative to the cobalt portion of a lithium-cobalt cathode is metallic foam. A number of metals are currently being tested by researchers and manufacturers.
WHY USE METALLIC FOAM FOR CATHODES?
A higher energy-density battery requires a cathode with a larger surface area. Foam is 3-dimensional and porous, so it provides more places for ion exchange to occur. This can contribute to faster charge times. Foam also has a stable, durable structure that is strong enough to easily attach a lithium sheet. Both thermal processes can be completed in a specially designed sintering furnace.
3. BATTERY ANODES: PREPARING PARTICULATE CARBON GRAPHITE
Furnaces can be used to prepare materials used to manufacture lithium-ion battery anodes. Material is heated to 800˚C in a controlled-atmosphere furnace chamber, which separates the hydrogen and carbon particles. The carbon is then graphitized via a separate process to create a mesocarbon for the anode.
Advantages of this method include the high purity of the resulting carbon particles, and the physical structure of the finished material, which creates a large surface area for the lithium.
4. VEHICLE LIGHTWEIGHTING: SINTERING AIDS WEIGHT REDUCTION STRATEGIES
>> Click here to watch this information >>
Making vehicles lighter results in higher fuel efficiency, longer driving range, and longer battery life. Many components within a vehicle, including drive and engine parts and gears, can be made lighter, and these have a cumulative effect on the overall weight of the vehicle. Some examples of how to reduce vehicle weight include:
- Manufacturing standard components with conventional but lighter materials (e.g., aluminum sheet metal instead of steel)
- Additive manufacturing with aluminum or other light metals
- Forming parts by compressing powdered aluminum or other light powder metals
- Adding holes to conventional part designs to reduce the amount of solid material
Parts can then be processed in a furnace to sinter, treat with steam or other gases, or delubricate as necessary.
It’s important to remember when the composition or design of a part is changed (e.g., powder metals, strategic holes) structural integrity or dimensional control can be compromised. For example, things like a tolerance for flatness, tensile strength, ductility, or toughness, must still be achievable in light-weight parts. Using a furnace that is customized to the process is an excellent way to ensure proper sintering, adequate delubrication, and that other critical steps are followed precisely, and all specifications are met.
TIPS FOR INNOVATION IN FUEL-EFFICIENT AND EV MARKETS
Innovation is all about finding new ways to use tools and materials to create a better product. As you develop, test, and refine applications geared toward fuel-efficient and EV vehicles, or products powered by AC motors or rechargeable batteries, keep these tips in mind:
- Consider using a multi-function furnace, which provides many options for temperature, atmosphere, and time spent in the furnace to prepare materials and parts to your exact specifications.
- Test out designs for AC motor parts in small motors such as bikes, scooters, small consumer products.
- Build good lines of communication between research and development and design teams.
- Focus on high-energy density materials for smaller size and reduced weight.
- Remember, every little bit helps when creating energy efficient vehicles: even tiny reductions in weight in a few components have a net effect, which in turn helps range development.
ADDITIONAL RESOURCES
- Sintering fundamentals
- Technical paper: A Review of Lubricant Removal Systems and the Latest Technology
- On-demand webinar: A Review of Lubricant Removal Systems and the Latest Technology
- Presentation: Advancements in Continuous Processing of Soft Magnetic Components
- Thermal Processing Magazine
- Heat Treat Today