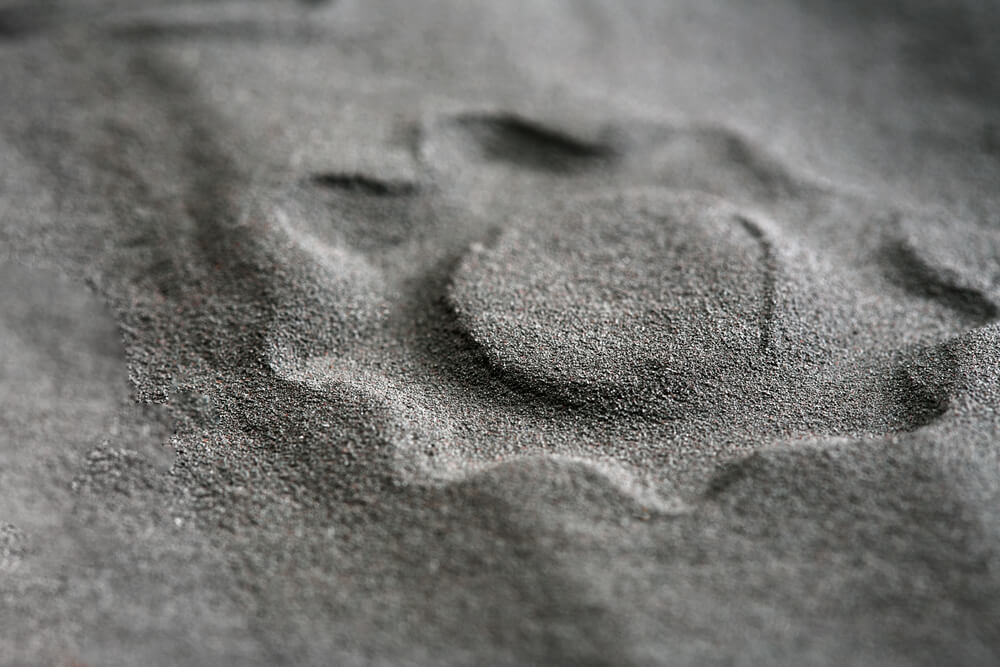
We often think of metals as solid sheets or blocks that must be cut or shaped with high temperatures or great force. Metals are also available in powdered form in a variety of particle sizes and shapes and they can be compacted into intricate 3D shapes, used in additive manufacturing, or applied to other surfaces as a coating.
This guide explains the basics of powdered metal materials and manufacturing processes.
What are powdered metals?
Powdered metals, as their name implies, are raw metals in finely powdered form. The powders can be combined with other metals, lubricants, binders, or colorants to create desired properties in finished components and for various applications.
Learn about the fundamentals of sintering (including for powder metal components) – click here to watch our video.
Process of producing powdered metals
While there are multiple ways to create metal powders, two methods are most common:
- Direct reduction/solid state reduction. Metal ore is ground or milled, then non-metallic materials are removed by passing the powder through a special sieve. The powder is often annealed in a furnace to increase ductility and reduce hardness, which results in improved compactibility and “green” strength (i.e., the part’s strength, after compacting but before sintering).
- Raw metal is heated and the resulting liquid is processed with high-pressure liquid, or in a centrifuge to create fine particles.
Additional methods include electrolysis and chemical treatments.
Comparing common powdered metals
Metals in powdered form retain the properties and characteristics they would have in sheets or blocks, and some properties can even be improved or altered with heat treatment.
Factors of conductivity, strength, density, weight and more
Depending on the application, properties to consider include magnetism, density, strength (which includes both “green strength” immediately after compaction or strength of the finished part after sintering or other heat treatment for hardening), ductility, or thermal and electrical conductivity.
- Iron/ferrous and carbon steel. While both can be used for structural components, carbon steel generally has higher strength and better machinability. They can be heat treated to improve properties like hardness, strength, and durability.
- Steel and stainless steel. Low alloy steel typically has good strength and durability properties, though it is often heat treated to enhance them. This material is also used for additive manufacturing and metal injection molding applications. Stainless steels are not as strong as other steel alloys; however, they have greater ductility and corrosion resistance.
- Aluminum. Heat treatment can improve aluminum’s strength; however, it generally has low ductility. This lightweight material is used in paints, sealants, electronics, solar panel components, as well as vehicle components.
- Nickel. Can be added to harden and strengthen ferrous materials. It has high luster as well as good corrosion and wear resistance. Tin also has excellent tensile strength and ductility.
- Bronze. Used in parts requiring high density and high strength, including bearings and bushings.
- Tin. Widely used thanks to its low melting point, electrical conductivity, solderability, and corrosion resistance. Common applications include electronics, lithium ion battery anodes, plating, and as a component in solder.
- Copper. With less strength than ferrous materials but greater ductility, copper is valued for its electrical and thermal conductivity. It can also be used with other friction materials to improve “grip” in automotive parts (e.g., brakes, clutches).
- Red cuprous oxide (Cu2O) and black cupric oxide (CuO). These oxides of copper are often used as pigments or colorants in coatings, enamels, and copper plating.
Applications for powdered metals
Powdered metals are used in several ways within the automotive, aviation, medical, and electronics industries. Parts made by powder metal manufacturing include many types of AC motor components, such as those in bikes and scooters, power lawn and garden equipment, and automotive systems (e.g., windshield wipers, automatic windows and doors, power antennas). Other products include brake pads, magnets, and soft magnetic parts.
The following are common manufacturing applications for powdered metal materials:
Compaction and Sintering
This common form of powder metal manufacturing has three basic steps:
- Pulverization and sieving. First, raw material metals are powdered, then mixed with wax lubricants and other binders to aid compaction and ejection from the mold.
- Die compaction. Next, the powder metal mixture is poured into a die and compacted with a press. Presses are hydraulic, mechanical, or servo-controlled and typically apply pressure from the top and bottom simultaneously. The size of parts made with this process is limited by the tonnage available in the press.
- Sintering and/or melting. Finally, the newly compacted or “green” parts are sintered in a furnace. Typically furnaces have three stages: lubricants are removed, the part is sintered to bond the individual particles, and the part is cooled or cured within an atmosphere-controlled chamber.
Additive Manufacturing/3D Printing
Powdered metals can be used in additive manufacturing processes with a special 3D printer. The metal powder is usually mixed with binder or other additive and “printed” in multiple thin layers to achieve the desired part. After printing, the part is sintered to remove binders and lubricants, and to strengthen the structure.
Metal Injection Molding
In this process, metal powders are blended with polymer binders to create a thick liquid base that is injected into a die. Once solid, the part is heated to remove the binder and sintered. The process is effective for shapes with complex part geometries; however, some part shrinkage occurs once the binder is removed and the part is sintered.
Chemical Processes
Solid metals were traditionally used as catalysts for certain chemical reactions; however, metals in powdered form provide more surface area than solid metal and speed reactions. Applications include battery electrodes and biofuel-powered engines.
Surface Coatings
Powder coatings are applied to parts electrostatically, then heat treated. Bonded metal powders can be added to the powder coating base to create a smooth and uniform metallic coating, and powdered metal oxides can be used to add color. It is a durable and cost-effective alternative to paint.
What are the advantages of powdered metal manufacturing?
Powdered metal manufacturing has several advantages over other types of metal forming. Because the metal particles are very fine, they can easily be molded and pressed into precise shapes or printed in multiple thin layers with a 3D printer. The tiny particles fill all available space in molds to create a contiguous material with no gaps.
It’s also possible to achieve intricate shapes with very little excess material to remove through secondary processes. This is often called near net manufacturing or NNM, in which the compacted or printed part is produced in exactly or very nearly its final shape after initial manufacturing. These methods usually result in minimal scrap and less wasted raw material, which saves money.
In addition, portions of the manufacturing process can be automated to increase throughput and improve workforce utilization. Examples include using robotics and automation equipment for:
- Filling compaction presses
- Machine tending (e.g., pushing buttons on a press or other equipment)
- Removing “green” compacts from molds
- Transferring compacts to trays with electromagnetic grippers (which can reduce handling damage)
- Loading and unloading parts from a sintering furnace
How is powdered metallurgy different from casting and forging?
Powdered metal manufacturing, and specifically the compaction and sintering process explained above, is often compared with both casting and forging. It is helpful to look at how these methods differ.
In casting, liquid metal is poured into a mold and allowed to solidify. Once released from the mold, the piece is further machined to remove excess material and perfect the part features and overall shape.
Casting can result in gaps or bubbles in areas of the mold where the liquid metal did not flow in fully, which may lead to inconsistent part strength or quality. Metals with low melting points, such as aluminum, magnesium, or zinc, are often used with casting. In contrast, metals with high-melting points, such as iron and stainless steel, are often better candidates for powdered metal manufacturing.
In forging, cold, warm, or hot metal is formed into a desired shape by pressing or stamping it with a die, hammering it, or rolling it. Parts made by forging are very strong because the metal’s grain is altered to match the shape of the part. Forging works well for large parts and in cases where precise control over the part’s microstructure is not required.
Contact Abbott Furnace Company today for powder metallurgy solutions
The Abbott Furnace Company team’s research and development work with powdered metal manufacturing has culminated in specialized furnace systems, such as the Vulcan delubrication system, which removes lubricant from green compacts prior to sintering. This is traditionally one of the biggest challenges in sintering green compacts without forming soot, which contributes to furnace damage and compromises part quality. Our furnaces can also be used for heat treatment of parts made via additive manufacturing or of metal powders prior to molding.
Industrial furnaces & atmospheric control
We can customize a multifunction sintering furnace for your unique powder metallurgy needs with regard to correct temperature ranges and atmospheres, as well as the length of time parts spend in each chamber. Continuous belt design allows for high throughput and efficient operations. Please contact us to learn more!