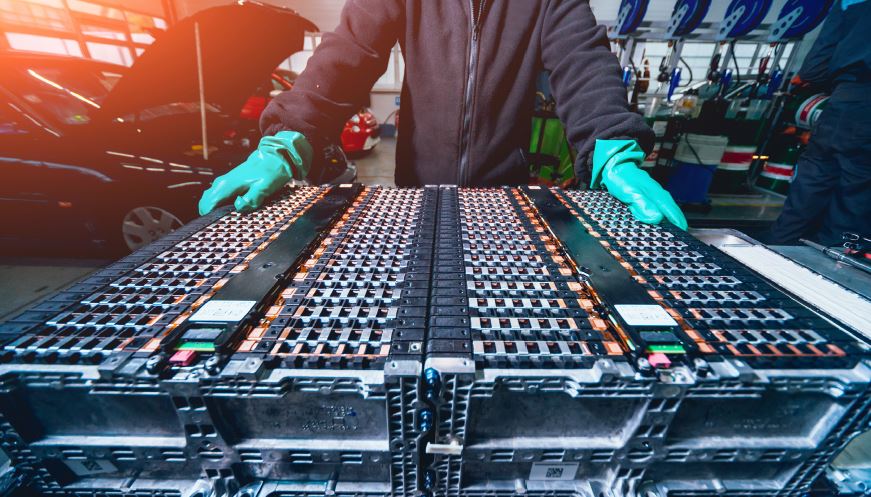
It’s no secret the world is transitioning from using internal combustion engines (ICE) to electric vehicles (EV) in various forms of transportation. There is a push to replace power generation by fossil fuels with the use of renewable sources to make electricity. High demand for battery materials exists to be used for Li-ion, LFP, NMC, NiMH, and numerous other chemistries. They cannot be produced quickly enough to support all mobility solutions and batteries used in energy storage systems (ESS).
Companies participating in electrification and decarbonization arenas seemingly grow overnight as funds become available through the Inflation Reduction Act (IRA) and significant investment by private equity. As key industry players develop materials for cathodes, anodes, cooling systems, and other battery or EV components, they uniquely position themselves for success within the electrification economy. The companies must produce their offerings in such a way as to reduce their cost per a given quantity while still maintaining high quality and consistency.
Many of these new materials are created in a laboratory setting using batch thermal processing equipment. Still, companies at the forefront recognize a need for continuous furnaces as they progress on to pilot plants and then full-scale commercialization.
Using a batch process requires an individual to load a given quantity of material into a chamber, initiate a thermal sequence (ramp up / temperature hold / cooldown), then hope the contents of this box meet desired specifications when the door is opened. A continuous furnace allows the user to manipulate the makeup and quantity of materials entering the input side while viewing the effects of a previous change on the output side.
Different forms of material can be processed in a continuous furnace. Solid objects often sit directly on the wire mesh of a belt furnace, while smaller items can be placed on plates to be indexed through a pusher furnace. Powder can be placed in crucibles for transport in a roller hearth kiln (RHK), or sometimes it is placed directly onto a solid belt made of a stainless strip.
As a result of the progression from ICE to Hybrid to full EV, thermal processes needed to support these emerging technologies must also progress. Processing each material effectively and efficiently requires knowledge of how individual constituents react to yield the desired results. Whether the process is activation, calcination, carbonization, oxidizing, pyrolysis, or sintering (to name just a few), each chemistry requires a thorough understanding and control of the time, temperature, and atmosphere inside the furnace to optimize material characteristics. Today’s thermal processing equipment must achieve high throughput while maintaining a low PPM of oxygen and minimal temperature variation.
Before charging headlong into the production of battery materials and EV components, contact Tim Raffeinner, Technical Sales Manager at [email protected] or 814-781-6355.