INDUSTRIAL FURNACE ARTICLES / BLOG
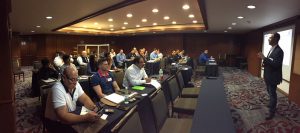
Abbott Furnace Company Announces Charleston Symposium Dates
Join some of the world’s experts in the brazing of carbon steel, stainless steel, brass, and aluminum. Abbott Furnace Company’s two-and-a-half-day symposiums cover brazing fundamentals, filler metals, joint design, troubleshooting, and the new AIAG CQI-29 – Brazing Special Process Assessment. Our symposiums are ideal for brazing engineers, maintenance personnel, product designer, and anyone involved in
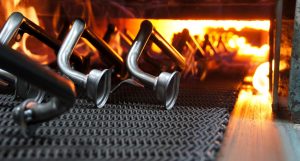
Recap of CQI-29 BRAZING SYSTEM ASSESSMENT WEBINAR
The new AIAG CQI-29 Brazing System Assessment specifies process requirements for an organization or its suppliers performing applicable aluminum and stainless steel brazing. Processes covered are CAB, Vacuum, Flame, and Induction brazing, and contain requirements for part print, control plan, braze quality inspection & reports, parameter documentation, maintenance records, sustainability, process monitoring, fixturing and tooling, and thermal management.
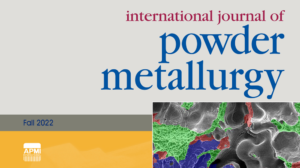
Amy McClain featured in IJPM
Abbott Furnace Company’s own Amy McClain was recently featured in the International Journal of Powder Metallurgy’s APMI Member Spotlight section.
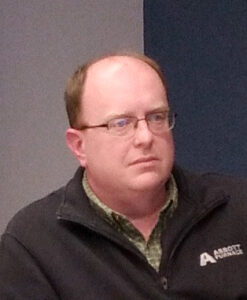
Dustin Yetzer elected to the PMEA Board of Directors
Congratulations to Dustin Yetzer who has been elected to the Powder Metal Equipment Association (PMEA) Board of Directors.
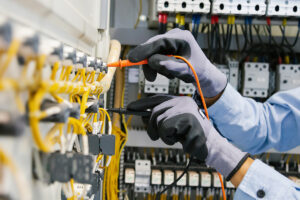
WEBINAR: Industrial Furnace Troubleshooting
INDUSTRIAL FURNACE TROUBLESHOOTING Tuesday, February 7, 202311:00 AM ET Join the industrial furnace engineering experts at Abbott Furnace along with our heat treating specialists and maintenance team for a Roundtable Discussion and Q & A session about troubleshooting your industrial furnace. You’ll have the opportunity to ask questions directly to the experts and receive answers
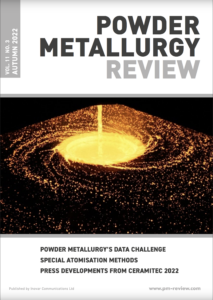
Lubricant Effects in Press & Sinter Powder Metallurgy
A paper co-authored by Director of Research & Development, Dr. Stephen Feldbauer, was published in the Autumn 2022 edition of the Powder Metallurgy Review. The article reviews the compaction and sintering effects of the four commonly used lubricants in Powder Metallurgy and Abbott’s Vulcan System, which enables complete lubricant removal. Read Article
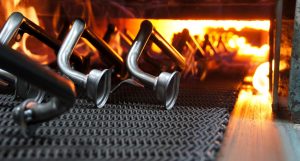
WEBINAR: CQI-29 Brazing Assessment
CQI-29 Special Brazing Assessment Tuesday, December 6, 202211:00 AM ET The new Brazing System Assessment specifies process requirements for an organization or its suppliers performing applicable aluminum and stainless steel brazing. Processes covered are CAB, Vacuum, Flame, and Induction brazing, and contain requirements for part print, control plan, braze quality inspection & reports, parameter documentation,
Job Opening – Industrial Painter
Abbott Furnace Company, a leader in the manufacturing of industrial furnaces, located in St. Marys, PA currently has an opening for an experienced and reliable full-time Painter. Responsibilities: All aspects of prepping, sanding, and applying professional finishes to our manufactured equipment. Requirements: High school diploma or GED. Experience with industrial and automotive paints and finishes.
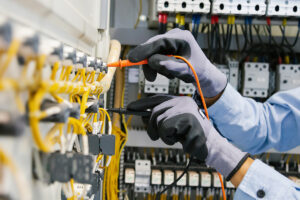
WEBINAR: Trouble Shooting Electrical Issues
Trouble Shooting Electrical Issues – A Round Table Discussion on Industrial Furnaces Thursday, August 4, 2022 11:00 AM ET PANELISTS: Dustin Yetzer – Applications Engineer Brian Smith – Applications Engineer Matt Pavlock – Field Service Manager Don Schnars – Technical Services
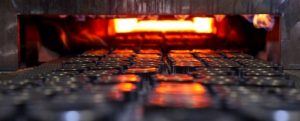
Mesh Belts vs. Rollers: Which is Better?
The choice of furnace belts for high temperatures will boil down to mesh belts and rollers. This article covers the advantages of both.
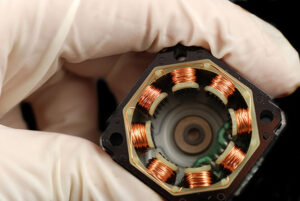
Soft Magnetics – What is it?
Learn how soft magnetics work, what they can do and why they are better than conventional steel magnets.
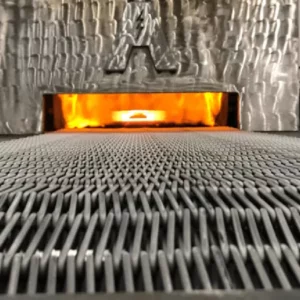
Why Continuous Furnaces?
Continuous Furnaces (also known as Continuous Belt or Conveyor Belt Furnaces) carry process parts or material through the primary heating chamber for rapid thermal processing. They are designed for fast drying products and are often a great choice for medium and high-volume part manufacturing. https://abbottfurnace.com/wp-content/uploads/2022/01/Why-Continuous-Belt-Furnaces_.mp4
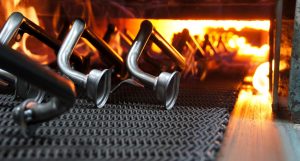
Industrial Heat Treatment Furnace Guide
Heat-treating is using rapid heating and cooling to alter the physical or chemical properties of metal or other substances. This is usually done to improve the metal’s hardness, strength, or ductility, but heat-treating can also be used to remove residual stress and increase wear resistance. Processes that rely on heat treatment include brazing, tempering, annealing, case hardening, normalizing and sintering.
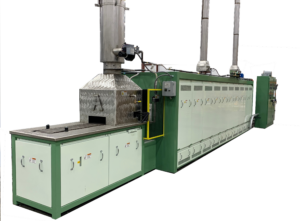
Save time and money with an all-in-one, continuous process for soft magnetic composites
An alternative method in the production of soft magnetic material is the Nautilus process – a dedicated, continuous process furnace that completes all the steps from lubricant removal through final steam treatment/curing. This process features convective heat, an appropriate delubrication temperature range of 350˚F to 1000˚F, and a separate chamber for atmospheric injection.
Binder Jetting 6061 aluminum and the importance of Abbott’s continuous furnace
Learn how Abbott and ExOne have partnered to deliver high-density, repeatable results in binder jet printing and sintering 6061 aluminum and the role that our continuous furnaces, such as the Vulcan, have as an essential part of the process.https://abbottfurnace.com/wp-content/uploads/2022/01/Binder-Jetting-6061-aluminum-and-the-importance-of-Abbotts-continuous-furnace.mp4
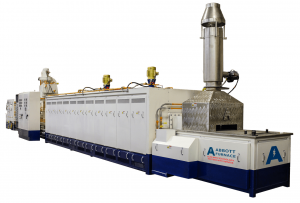
Lubricant Removal Systems and the Latest Technology
Lubricant removal has been one of the major problems in the production of powdered metal components. But now, there has been a paradigm shift in how they are removed.
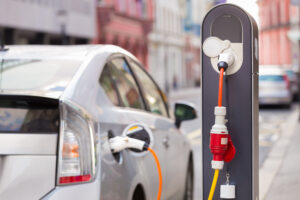
Advancements in Continuous Processing of Soft Magnetics
With the electrification of our world ever-growing, the application of soft magnetic components is rapidly increasing. A novel, new approach was developed to produce soft magnetics in a continuous process that is more efficient and cost-effective.
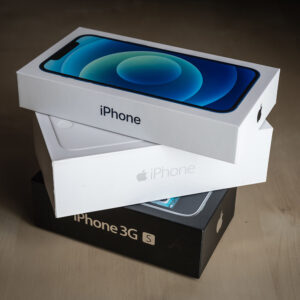
Molded Pulp Packaging is Versatile Across Many Industries
Molded pulp (molded fiber) is a versatile multi-tasker in the world of packaging materials. Manufacturers across industries use it to protect many types of products.
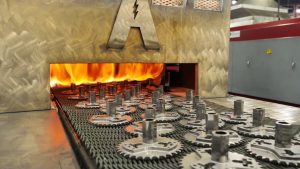
Industrial Furnace Troubleshooting – 14 Issues Resolved
PANELISTS: Dustin Yetzer – Applications Engineer Brian Smith – Applications Engineer Matt Pavlock – FieldService Manager Don Schnars – Technical Services Our furnace experts answered 14 of your most burning questions about industrial furnace troubleshooting, maintenance, repair, and emergency situations. This video will also teach you how to recognize problems early, accurately diagnose and troubleshoot
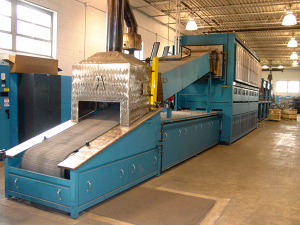
A Guide to Industrial Furnace Features and Types
The configuration of equipment and engineering that goes into a furnace impact the quality of the parts coming out. Here are the basics you need to know.
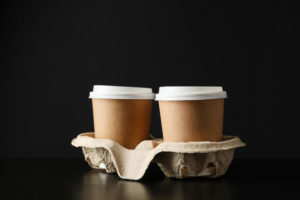
How are Molded Pulp Molds Made?
Molded pulp packaging guards against breakage, vibration, and shifting. Molded from wet fibers, it has a snug, secure other options cannot match.
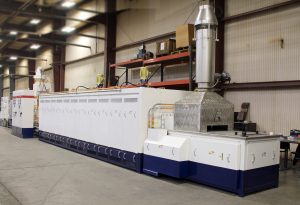
Controlling Atmosphere and Air Flow in Industrial Furnaces
Learn how to produce precise & repeatable results by carefully controlling furnace atmospheres, temperatures and air flow in industrial furnaces.
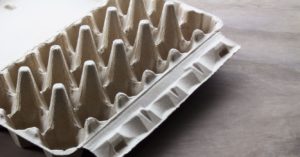
Inside the Fiber Pulping Process for Molded Pulp Products
There’s more than one way to prepare fibrous raw materials for use in molded pulp products. This blog takes a closer look at the processes involved.
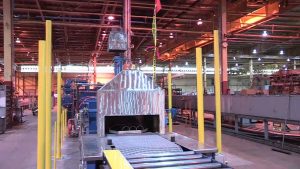
How to Design an Industrial Furnace for Your Application
There are different types of furnaces for different types of applications. Read this blog to gain a better understanding of the industrial furnace and components you’ll need.

A Guide to Powdered Metal in Manufacturing
Powdered metals are used for many manufacturing applications. Our guide explains what you need to know about how they’re made and put to use.
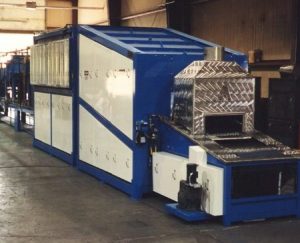
A Guide to Industrial Furnace Maintenance
Is your furnace running smoothly? If not, this guide will help you troubleshoot any maintenance problems that may arise in your industrial furnace.
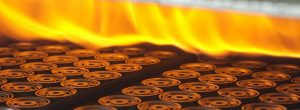
Save Time & Money with an All-in-One, Continuous Process for Soft Magnetic Composites
Soft magnetic composites drive electrification in many applications. Continuous process furnaces keep them cost-effective and efficient to manufacture.
Abbott Furnace featured in October issue of FFJournal
FFJournal Senior Editor, Lynn Stanley authored a piece entitled “Impossible Mission Force” about Abbott’s partnership with The ExOne Co., a leading designer, and builder of binder jet 3D printing technology, and Ford Motor Co. to develop a continuous belt furnace that could successfully sinter binder jet 3D printed aluminum 6061 and demonstrate the equipment’s ability to
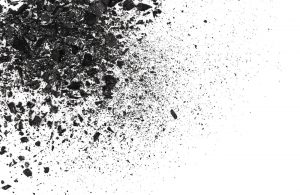
Remove Lubricant, Eliminate Soot, and get a better sinter in a single process
A furnace with special features and integrated controls to remove more lubricant, create less soot, and achieve a better sinter.